Foam Conversion: Transforming Versatile Materials
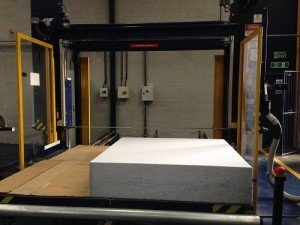
Foam conversion is the process of transforming raw foam materials into customized products tailored to meet specific industry needs. This transformation can involve cutting, shaping, laminating, or assembling foam components to enhance functionality. Whether for insulation, packaging, or bespoke acoustics, foam conversion plays a crucial role in multiple industries, including automotive, marine, construction, and medical sectors.
The Foam Conversion Process
Foam conversion involves several advanced techniques and machinery to ensure precision and quality. Some of the key processes include:
- Band Saw Cutting: Used for slicing foam into specific thicknesses.
- Profiled Slitting: Allows for intricate shaping of foam sheets.
- CNC Profiling Machine: Provides precise custom designs for bespoke acoustics.
- Laminating: Bonds foam layers to enhance durability and functionality.
- Water Jet Cutting: Uses high-pressure water jets to create complex designs without damaging the material.
- Die Cutting: Enables mass production of foam components with consistent dimensions.
By leveraging these techniques, foam conversion companies like Acoustafoam can transform standard foam into highly technical products, addressing unique acoustic and insulation challenges across various industries.
Types of Foam Used in Conversion
Different types of foam are utilized depending on the intended application. Some of the most commonly used foam materials include:
- Polyurethane Foam: Found in mattresses, cushions, insulation, and packaging.
- Polystyrene Foam: Lightweight and insulating, often used in packaging and disposable containers.
- Polyethylene Foam: Known for its durability and moisture resistance, making it ideal for padding and protective packaging.
- Class 0 Foam: Fire-resistant and acoustically efficient, widely used in high-risk environments such as engine rooms and heavy vehicles.
Each foam type has unique properties that make it suitable for different industrial applications.
Applications of Foam Conversion
Foam conversion finds applications across a variety of sectors, enhancing product functionality and performance. Some of the primary applications include:
1. Acoustic Solutions
Foam is widely used in bespoke acoustics to minimize noise pollution and enhance sound quality. Acoustic foam panels help absorb sound waves, reducing echoes and background noise in environments like recording studios, home theaters, and industrial workspaces.
2. Automotive Industry
In the automotive sector, foam conversion is essential for producing interior components such as headrests, seat padding, and door panel insulation. These components contribute to both comfort and noise reduction in vehicles.
3. Construction and HVAC
Foam plays a significant role in the construction industry, particularly in soundproofing and thermal insulation. HVAC systems also benefit from foam insulation to enhance efficiency and reduce noise generated by ventilation units.
4. Medical Sector
Medical foam conversion is used to manufacture orthopedic supports, hospital mattresses, and cushioning for medical equipment. Foam’s adaptability ensures patient comfort and safety.
5. Marine and Boats
Bespoke acoustic foam solutions are widely used in marine applications, providing soundproofing for engine rooms, cabins, and generator canopies. Foam materials like Class 0 profile foam offer excellent sound absorption while meeting stringent fire safety standards.
6. Packaging and Material Handling
Custom foam packaging solutions protect fragile items during transportation. Polyethylene foam is particularly useful for shock absorption and moisture resistance, ensuring goods remain secure during transit.
Benefits of Foam Conversion
1. Customization for Specific Needs
Foam conversion allows industries to create products tailored to their unique requirements. Whether for bespoke acoustics, medical applications, or automotive components, foam can be shaped and fabricated for precision.
2. Enhanced Soundproofing and Insulation
Acoustic foam solutions help reduce unwanted noise, improving comfort and productivity in workspaces. Additionally, foam’s insulating properties contribute to energy efficiency in construction and HVAC systems.
3. Durability and Safety
Many foam products, such as Class 0 fire-resistant foam, are designed to withstand harsh environments, offering longevity and compliance with safety regulations.
4. Eco-Friendly Options
Some foam conversion processes incorporate recycled materials, reducing environmental impact and promoting sustainability.
5. Cost-Effective Production
Foam conversion enables mass production of components at competitive prices, making it an affordable solution for industries requiring high volumes of customized products.
Quality Control in Foam Conversion
Ensuring the highest quality standards is essential in foam conversion. Leading manufacturers implement rigorous quality control measures, such as:
- Material Testing: Assessing foam properties to meet industry specifications.
- Dimensional Accuracy Checks: Ensuring precise cuts and designs using CNC profiling and die-cutting.
- Fire and Safety Compliance: Verifying that foam products meet fire-resistant and safety regulations.
- Customer Specifications Adherence: Producing foam components tailored to client requirements.
Companies like Acoustafoam adhere to ISO 9001:2015 standards, ensuring high-quality products that meet diverse industry needs.
Read also: Understanding Pigging System Applications in Modern Industries
Conclusion
Foam conversion is an essential process that transforms raw foam materials into functional and high-performance products. From bespoke acoustics in recording studios to fire-resistant foam for industrial applications, the versatility of foam makes it a valuable resource across multiple sectors. With advanced manufacturing techniques, quality control measures, and an emphasis on sustainability, foam conversion continues to drive innovation and efficiency in modern industries.
For businesses seeking customized foam solutions, industry-leading experts like Acoustafoam provide tailored services to meet specific needs. Whether for automotive interiors, medical cushioning, or marine soundproofing, foam conversion remains a fundamental aspect of product development and performance enhancement.