Best Practices for Extracting and Processing Metals in Mineral Refineries
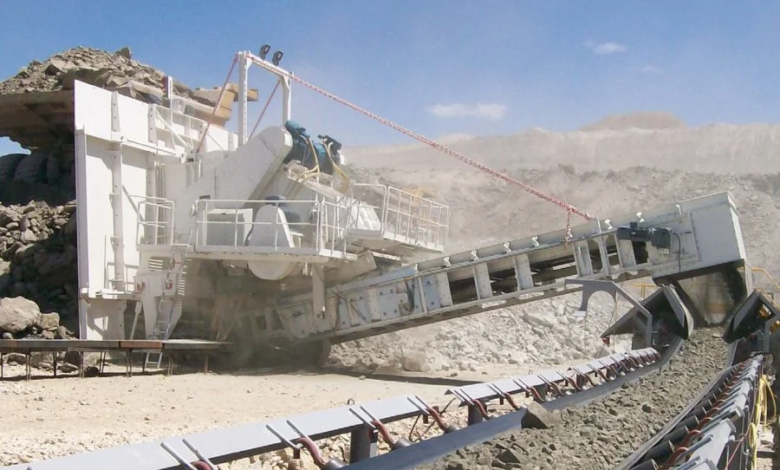
Gaining access to and processing metals from their respective ores greatly benefits from possessing specialized technologies, tools, as well as expertise. In striving to meet operational goals for a B2B enterprise in the mining and refining sectors, the provision for effective and efficient practices alongside cost-control measures greatly benefits the quality of metal extraction. We will concentrate on the best practices regarding the procurement and refining of metal in a mineral refinery plant, addressing the major issues of productivity and performance with regard to some important technologies and techniques.
Selecting the Right Equipment
The most important component of any successful extraction equipment process is the correct division of apparatuses. Choosing equipment does have an impact in mineral refineries as it does in other businesses undertaking metal fabrication. The right machinery ensures that ore is effectively processed while losing no precious metals. A stone horizontal impact crusher, for example, is perfect for dividing large ore parts into smaller pieces that are more manageable and easier to derive valuable metals from. Additionally, shaker tables, which are used to enhance the overcoming of concentrating metal ores by separation of lighter waste materials, help achieve better recovery of lower grade minerals.
When obtaining apparatuses for metal extraction, a number of parameters like the type of ore, the throughput that is planned for, as well as the influence on the environment have to be thought of.
Specialized equipment flotation cells, gravity separators, or leaching tanks, for example, may be required when working with complex ore bodies or those with a high level of impurities. Metal refineries can meet production and regulatory requirements in an efficient manner by working with reputable equipment suppliers.
Enhanced ore preparation augments the refinery’s productivity by ensuring that only appropriate materials are fed into the different stages of processing.
See also: Payroll Outsourcing Singapore: A Cost-Effective Business Solution
Optimizing Ore Preparation
Separation techniques are very important in extracting precious metals in waste during the refining process. The mineral refineries employ a wide range of methods including gravity separation, flotation, and magnetic separation to increase the recovery of the metal and simultaneously maximize energy efficiency. One of the most common methods employed in fine separation of metals is the shaker table. Shaker tables work mainly on the principle of motion as well as gravity whereby heavier particles are agitated and separated from the lighter materials ensuring effective concentration of precious metals such as gold, silver or copper.
Flotation is also an important separation technique where special chemicals are used to produce bubbles in water where certain types of minerals are intended to be collected so as to float. Flotation works effectively for some ores with sulfide minerals or those with small sized particles. In combination with carefully selected separation methods, metal refineries are able to achieve the desired metal purity and efficiency in operations.
With the goal of maximizing metal recovery yield, it is also helpful to have novel technologies that automate the monitoring and control of the separation process.
Shifting human tasks to machines minimizes the possibility of making mistakes, facilitates refining accuracy, and guarantees that even multifaceted or specific ores are processed in an orderly manner.
Implementing Efficient Separation Techniques
Metal refineries focused on best practices ensure that their processes are environmentally compliant. As metal extraction and refining is usually accompanied by, it does impose a heavy burden on the environment in terms of water and air pollution along with the waste it generates. Such effects on the environment can be greatly reduced and effectively controlled through the application of environmentally compliant technologies and processes.
For instance, the implementation of water reclamation systems in the refinery assist in conserving water and lessening the volume of contaminated effluent that is produced. Furthermore, devices to control air pollution such as bag filters and scrubbers that help in the control of dust during the crushing and grinding activities, increase the chances of reducing air pollution. Besides, tailings waste management methods provide an opportunity for refineries to reduce waste by keeping or reusing waste materials for other activities.
Ensuring Environmental Compliance
Fulfilling environmental obligations covers the industries need to comply with government set regulations and provides support for sustainability practices throughout. Business practices practicing environmental care are more likely to attract new investors, develop good relationships with industry stakeholders, and lower their long term expenses as a result of environmental negligence.
Continuous Monitoring and Optimization
The mineral refinery’s strides are facilitated by monitoring and periodic optimization of processes and other operational activities.
The extraction and processing of metals are complex activities, and the smallest deviations in the quality of the ores and the performance of the equipment that is used can reduce the productivity of metal recovery and productivity as a whole. The extraction and processing of metals also requires continual monitoring and control systems that track KPIs in real time in order to ensure consistent output.
Process automation and control systems are capable of measuring and controlling temperatures, pressures, flow rates, and even the sizes of particles, which allows them to run certain operations automatically. Also, predictive maintenance can be performed to estimate the time to failure of the equipment so that scheduled maintenance can be performed, which minimizes the time lost and resources spent to conduct unscheduled repairs. Through the use of real time monitoring and perpetual optimization, refineries stand to gain improved efficiency, less waste, and a higher quality of the final product of the metal.
Tools that analyze and extract usable insights from performance data also help in pinpointing inefficiencies. By optimizing the refining procedures, the B2B enterprises are able to be competitive and supply the almost inexhaustible demand for high grade metals in various industries.
The refining of metals extracted from ores is best achieved with proper selection of machinery, strategic ore treatment, effective separation techniques, process monitoring, and environmental friendliness and compliance.
There is little doubt that the adoption of these practices can enhance the recovery of metal, minimize costs, and optimize the sustainability of operations in the long run. The horizontal impact crusher and shaker tables, as well as automation and process control, facilitate the high output and brand of productivity and metal extraction that are required. These days the mining sector has to be more efficient, environmentally responsible, and make more profit than ever before, so B2B companies in the refining business have to develop new techniques and approaches in order to remain competitive on the global market.