The Basics of Pneumatic Systems: How They Power Modern Machinery
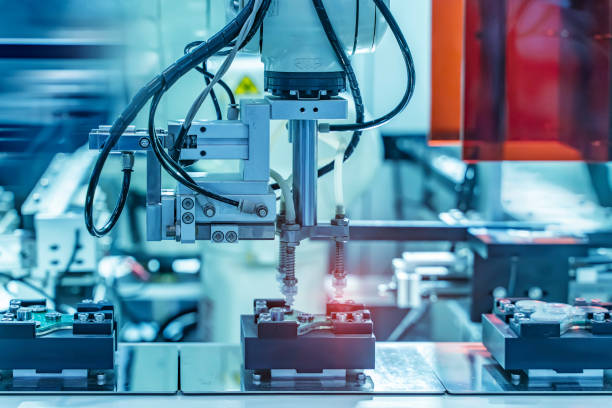
These systems are indispensable parts of automation in any industry because they allow accurate and non-contact object sensing in many applications. In the case of manufacturing, packaging, and even material handling, power transmission via pneumatic systems is a common and efficient way of utilizing compressed air. Electric and hydraulic power systems have batteries, cables, and fluid reservoirs as their energy storage systems, while pneumatic systems use compressed air. These systems offer easy detection of objects without direct contact. That is why, in industries utilizing automation, tremendous savings can be accomplished in saving energy while still being fast and all-encompassing. This article describes how the components of the pneumatic systems work, how they are used in an industry setting, and how modern industrial automation supply houses make these systems effective and efficient for a variety of uses. The benefits of energy efficiency, speed, and flexibility have made these systems a mainstay for industries that needed a greater amount of automation.
What is a Pneumatic System?
A pneumatic system is defined by the use of compressed gas to do physical mechanical work. These systems comprise compressors, actuators, valves, piping, and an entire range of other components. The system works by transforming the energy in compressed air into mechanical energy that drives tools and equipment. Pneumatic systems are widely used in various practices where precision electronics or heavy-duty hydraulics systems are too cumbersome, can be used in dangerous environments, can support low-weight objects, and allow for quick and accurate movements. These systems make use of air under pressure to actuate pistons, cylinders, or motors that perform work. This energy is further utilized to drive machinery such as conveyor belts, presses, robots, and hoisting tools. Nowadays, most pneumatic systems in industrial use are found in the areas of high-speed accuracy, such as in packaging, handling, and other automation processes. Industrial automation supply companies provide these systems in different industries for the smooth functioning of various processes. Properly implemented pneumatic systems help industries like this to achieve their goals, such as high concentration of output with good quality and low operating costs. The versatility offered by these systems enables practically all industries to get the most out of it.
See also: Navigating the $84 Trillion Wealth Transfer: Essential Estate Planning Strategies
Elements of a Pneumatic System
The system is defined as a collection of items working together as a mechanism for efficient power propulsion. The key elements are compressors, air treatment units, actuators, and control valves. The compressor is the first element of the system responsible for compressing air from one’s environment and keeping it under pressure until it is needed. A system cannot function optimally without proper air treatment, which includes removing unwanted particles, controlling airflow rate, and adding oil to enrich the air. Next, the actuators, which are in the form of cylinders and pneumatic motors, transform the compressed air into mechanical energy to run the machinery. The last components are control valves, which determine the direction and volume of the compressed air in the system so that adequate power can be directed to the actuators when required. Some valves set a certain amount of power and control use at specific phases of the process, for example on or off. With the increase in the number of industrial automation companies, which focus on maintaining such systems, a higher degree of accuracy towards the entrapment of the items for minimum wastage is achieved. This gives the greatest flexibility and efficiency to the new industry.
Benefits of Pneumatic Systems
The major profitable gain of these systems is that their installation and cost is generally low relative to the required resources for electric and hydraulic systems. Vertical or horizontal motion needed for drilling, transporting, loading and pressing operations are easily achieved with these systems. Also, pneumatic systems are extensively used in applications where the risk of electrical sparks creating fire is high. Additionally, they are devised for tasks where it is essential to keep the surroundings clean or free of contamination such as food and drug industries. Safety with the non-use of other systems and the smoke-free usage of pneumatic systems gives safety in many aspects. Moreover, unlike hydraulic or electric systems, there is no need for moderation in angle adjustment or difficulties during monotony. Besides, there is also no struggle with delay as these systems complete tasks as soon as they are set. Therefore, applying these systems nurtures a high level of automation, precision, and speed for food, packaging, medicine, automotive, and electronics industries.
The compact nature of pneumatic systems means companies can save energy, floor space, and even costs, which makes systems attractive to companies that wish to optimize for space.
Pneumatic System Applications In Modern Equipment
Today, different pneumatic systems find applications across many industries. In manufacturing, powered pneumatic systems are very important in driving robotic arms, conveyors and assembly lines. Pneumatic systems can also be found in a myriad of actuators, tools, machines, and equipment lifts which are usually powered pneumatically and enable effective production through speed and power. There is also an incorporation of pneumatic systems in the automotive industry, mostly in the tire changers, assembly line hydraulic presses, and robotic welding arms. Pneumatic systems for food processing and packaging have similar functions in material handling or processing. Such systems serve a steady flow of products swiftly and efficiently, and resolve sanitary issues themselves. In construction and mining, pneumatic powered drills, hammers and even excavators have always been preferred for their light and sturdy form factor. The scope with which pneumatic systems can be used is versatile, from automated packaging systems and light industrial tasks to heavy machinery. These systems provide high-speed operation for machinery and offer precision at a low cost. Compressed air use opens doors for easy automation in industrial functions, therefore, pneumatic systems are an integral concern for industrial systems and are constantly revised with respect to technological progress and operational enhancement.
Conclusion
In industrial plants today, pneumatic systems are almost indispensable. They offer reliable, cost effective and efficient solutions to the problems of powering machines. Pneumatic systems perform mechanical functions like lifting, moving, and pressing by means of compressed air which makes operations faster and more accurate. The primary elements of pneumatic systems, including compressors, actuators, and control valves, ensure efficient operations within different industries. Partnering with industrial automation supply companies enables the businesses to get the best tailored pneumatic solutions to their specific requirements. These systems are very important to modern machinery including those used in manufacturing activities, packaging, food processing, and even construction work. Pneumatic systems are once again at the forefront as they utilize compressed air to enhance industrial processes and at the same time improve safety and sustainability in the workplace. With the rise of new emerging technology, it is believed that the need for pneumatic systems will continue to evolve as well due to the increasing demand for environmentally friendly energy solutions with high versatility.